Blog
What Manufacturers Should Know About CD Stud Welding
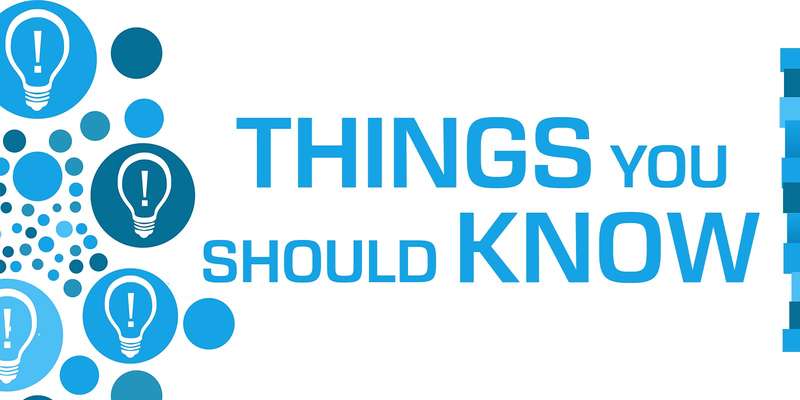
Understanding Capacitor Discharge (CD) Stud Welding
In stud welding, there are two main processes: Capacitive Discharge (CD) stud welding and drawn arc stud welding. Capacitive Discharge (CD) stud welding is a proven technology that has been in use for over 50 years. The broad range of use and applications is appealing to those looking for a fast, easy, and versatile process. The equipment is generally small and operates off of low voltage (110V or 240V in North America, 220V in Europe). Fasteners designed for CD welding typically have a flange formed on the weld end in conjunction with a tip that initiates the discharge arc and subsequently vaporizes once electrical current is applied. The re-solidified flange enables a strong weld.
The CD Stud Welding Process
To perform a weld using a CD stud welding system and a CD weld stud, you begin by loading a weld stud into its appropriately sized chuck or collet attached to the welding gun and then placing the welded end against the metal substrate it will be welded to. The power supply will then communicate with the gun, raise the stud slightly from the substrate, and send an electrical current stored in the capacitor to the metal piece and fastener. The heat resulting from this arc melts the metal substrate as well as the tip and collar of the fastener. For the fraction of a second the fastener end and mating substrate are molten, a spring within the gun plunges the fastener into the substrate strongly fusing them together as they cool.
Gap vs. Contact Technique
There are two primary techniques for CD welding: Gap and Contact. Both gap capacitor discharge welding and contact capacitor discharge welding are based on the same general principles and methods; however, there are differences in the process that are important to understand.
Contact CD Welding Summary
The process of contact CD welding starts with the operator positioning the CD studs in the correct location and pulling the trigger on the gun. This causes an electrical pathway between the gun and the metal piece. Pulling the trigger results in a short circuit, which causes a discharge of the capacitors that vaporizes the tip of the stud. This vaporization creates an arc that melts a small amount of the base metal as well as a bit from the bottom of the stud.
While this melting occurs, a spring in the gun simultaneously thrusts the stud down and into the molten material of the base metal. The molten material then rapidly cools, welding the stud in place permanently. The entire process takes 0.012 seconds to complete.
Gap CD Welding Summary
The contact CD stud welding process is not effective With both softer materials and materials that melt and cool fast, such as aluminum.,. Gap CD welding can avoid these issues by accelerating the stud quickly into the molten pool. This also reduces the weld time by about half.
With this process, the stud weld gun accelerates the stud towards the substrate or workpiece with precise timing and pressure. When the trigger is pulled, the stud is moved towards the base metal, and, as soon as it touches, the power source provides the energy needed to vaporize the tip and create the arc while at the same time fusing the capacitor discharge studs to the workpiece.
Welding Aluminum With CD Stud Welding
Aluminum can be a tricky material to weld as aluminum is both thermally and electrically conductive. This essentially means that aluminum conducts heat much better than steel or stainless steel alloys. This can present quite the challenge in welding, given that the heat input from the welding power source is quickly conducted away from the weld zone. When you conduct the heat away from the weld zone to some other area of the material, the weld zone does not stay hot enough to form a quality weld.
The aluminum workpiece must be properly prepared for welding, which is the same for both stud welding processes. Aluminum quickly forms a surface oxide, which is tough, nonconductive, and quite detrimental to quality welding. At Image Industries, we recommend cleaning with a stainless steel wire brush as carbon steel brushes leave deposits on the surface of aluminum which prevents successful welding. This cleaning process should be done within a couple of hours of actual welding. Otherwise, the oxide layer begins to form again.
When using the CD welding process, the weld times are short, around ten milliseconds. Short weld times are beneficial when
Cable Management
Cable management has been a problem for as long as there have been cables. But now, there is a breakthrough cable management solution that is fast, affordable and simple. Several options on the market address
When it comes to
CD ground studs can be used wherever a ground touchpoint is required. Image Industries offers CD ground studs that are designed to make it easy to establish a ground connection where you need it.
Grounding
Almost everything built today has some sort of electronics. Common items that are grounded are enclosures (cabinets and doors), cars, earthmoving equipment, and appliances; almost anything you can think of has grounds to the chassis. The electronics in these devices need to be electrically grounded to make sure they operate at the correct voltage levels and to prevent spurious electrical noise from entering the sensitive electronics.
Historically, grounding has been accomplished in many different ways:
- A hole drilled with a grounding stud through-bolted
- An extra tab welded to the structure with a cross-drilled hole
- A
threaded stud welded in place - A drilled and tapped hole
While all of these approaches certainly work, none are particularly elegant, and some are very costly. Our ideal grounding solution would be:
- Quick to install (low labor cost)
- Inexpensive (piece cost)
- Reliable (welded joint vs. friction)
- Easy to mask for painting
- Offer quick connection for wire harness installation
Image Industries offers a Capacitor Discharge (CD) weld stud that welds in place in less than one second, is low cost, and has an industry-standard male ¼” quick connect. The industry standard quick connect allows for easy masking and for simple and reliable harness connections.
The capacitor discharge weld stud installation is simple. The operator inserts the special quick-connect grounding stud into the stud welding tool chuck. They will then place the tool against the work, press the trigger, and in 1/10 of a second, the grounding stud is welded in place for a secure connection that will not loosen over time. This solution is low cost, reliable and quick. It also has an elegant, professional appearance that shines.
Examples Of CD Stud Welding Applications
The short weld time makes the process of CD stud welding invaluable. Aside from the actual material handling (loading new studs, moving locations, etc.), which tends to be the slowest part, this process also lends itself well to automation, increasing the predictability of quality. Adding to the benefits of the short weld times is that the penetration into the base material is roughly .0002 to .006 inches.
This incredibly shallow depth means that welding can be done with very little distortion to the reverse side of the workpiece. Additionally, due to the speed of the CD stud welding, minimal heat is used on the weld zone, causing no damage to coatings and finishes on the reverse side of the workpiece. This blemish-free application is crucial when cosmetic appearances are paramount.
Here are some common applications of capacitive discharge stud welding:
Control Panels
As a prime example of minimal damage to the reverse side, elevator buttons are typically held on with CD weld studs. From the front of the finished plate, we only see buttons, unaware of the attachments and welding on the other side.
Food Service Equipment
Sneeze Shields, a blessing on salad bars, are typically secured to the framework with CD studs. After these studs are welded to the structures, Plexiglas is then placed over the studs and secured with decorative nuts.
Signs
Finally, CD studs are welded to the backside of letters or to the total sign to secure the sign to the building.
Common Obstacles of Capacitive Discharge Stud Welding
Though there are many benefits to using the capacitive discharge (CD) stud welding method, it is not meant to be utilized with every application. Here are some of the potential obstacles to CD welding:
Positioning
Many customers like to locate the weld stud with a center punch mark. This center punch mark forms a small, localized valley in the sheet metal. While this is a successful way to locate the stud, it adversely affects the welding. The ignition tip can “sit down” in this valley, effectively making the tip length shorter. If a standard tip is about .03 inches long and the center punch mark is .015 inches deep, you have effectively shortened the arc time by 50%. With the ignition tip length so critical to consistent weld performance, it is bad practice to use center punch marks for CD welding. One common method to address the positioning of CD weld studs is to create a non-conductive stud positioning template above the substrate to be welded.
Surfaces Used
Due to the rapid speed of CD stud welding, the amount of arcing time spent melting metal is significantly less. If the surface is rough (think structural steel), the arcing time will probably not be sufficient enough to melt all the high points, allowing a high-quality weld. Additionally, if the surface has contamination like rust, mill scale, oil, or paint, the short arc time will not be able to adequately burn those contaminants away, resulting in a weld failure again. Most cold rolled sheet metals are very good candidates for CD stud welding.
Material Type
Again, we find ourselves dealing with the necessity of sufficient arc time. Because medium and high carbon steels are more difficult to penetrate, the short arc time makes this an almost impossible application. And with the same going for high tensile and hard materials, it is better to use drawn arc stud welding in these situations. Low carbon steels and stainless steels are ideal candidates for CD stud welding.
Plating
Simply put, CD stud welding works great on plating as long as the plating is capable of being welded. Unfortunately, this means that CD welding is a poor choice for zinc-plated materials, such as sheet steel or zinc-plated parts. Conversely, copper plated or nickel plated substrates are ideal for CD stud welding.
Size
If you find that you need a larger fastener for strength requirements (above 3/8 inches), then drawn arc stud welding is more appropriate than CD welding Certainly, in specialized applications, CD welding can go above 3/8, but for all practical purposes, CD stud welding maxes out at 3/8 Inches. The CD process maxes out a 3/8 because the energy required becomes very large very quickly.
Contact Image Industries For More Information
Like most things in life, a one size fits all approach is simply not the answer. Different approaches, techniques, and applications will be used in various scenarios. For many situations, capacitive discharge stud welding is the ideal technique. Yet, one must be aware of the limitations to guarantee success.
One other important thing to note is that all of the applications above utilize CD stud welding for aesthetic purposes. So the next time you have an application that is cosmetically sensitive, consider using the fast, reliable process of capacitive discharge welding with Image Industries. We’ll provide you with all of your CD welding needs, from equipment to accessories and weld studs. For more information, call Image Industries at (866) 944-0335 or request a quote online today.
Building lasting bonds since 1976.
Providing superior stud welding and stud welder parts and equipment isn't enough. We also strive to deliver better service and unmatched expertise. And that's exactly what we've been doing for more than 40 years.
Read About Our History