Blog
What Factors Should Be Considered When Choosing Weld Studs for a Project?
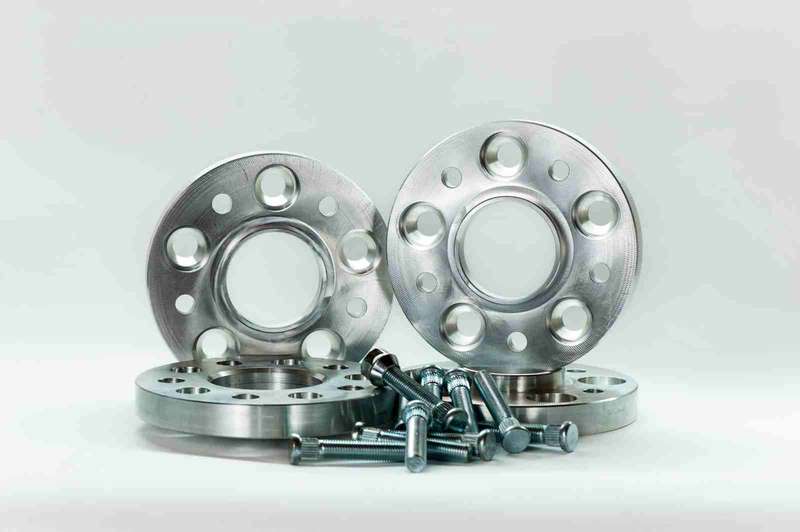
With this in mind, various factors need to be considered, including the types of materials you're working with, the welding techniques available, and the specific demands of your application.
In this article, we're going to carefully break down all of the essential criteria that you should think about when choosing weld studs, such as material compatibility, required mechanical properties, and the environmental conditions the studs will face.
Weld Stud Types
Let’s take a closer look at and contrast the two main weld stud types against one another to help you decide on the weld stud type you need based on the intended use and application at hand.
Drawn Arc
Drawn Arc weld studs are essential in the construction and manufacturing industries due to their strength, durability, and high degree of versatility.
These studs are typically utilized where strong, durable joints are required, and they’re known for their ability to create strong welds that can withstand significant stress and environmental conditions.
- Full Thread: Fully threaded arc studs are the most prevalent type out there today that are used extensively across thousands of applications. These studs offer excellent pull-out strength and are often employed in situations where the full length of the stud needs to engage with the mating material, providing a secure and durable bond.
- Partial Thread: Partially threaded weld studs provide a distinct advantage in terms of shear resistance compared to fully threaded studs. By concentrating the threads towards the end of the stud the non-threaded portion can bear greater loads, making them ideal for applications requiring enhanced shear capacity.
- No Thread: No thread weld studs are used where the primary requirement is the weld itself without the need for screw engagement. These are typically used in applications where the stud serves an important role in transmitting load or energy across the weld but does not need to be fastened into the base material.
- Collar Studs: These studs are generally used as standoffs for wire routing, plate spacing, and other applications that require a specific distance or offset between components. The collar provides a stable base that ensures the stud remains upright and properly aligned during and after welding.
- Collar Studs Right Angle: Right angle collar studs are an adaptation designed for scenarios where mounting surfaces aren’t conducive to straight studs. These studs are particularly useful in tight spaces or where components must be mounted perpendicular to the main assembly.
- Full Base: Full base studs offer the maximum shear resistance for their given thread size. The wide base of these studs disperses the load over a greater area, which is vital in applications where joint integrity and strength are paramount.
- Reduced Base: Reduced base studs are tailored for use in designs where space is limited and the full collar of weld flash cannot be accommodated. These studs still provide strong performance but fit into tighter spaces, making them suitable for compact designs where every millimeter counts.
The drawn arc weld stud is a versatile component designed to cater to diverse structural and operational requirements across various industrial applications.
At the end of the day, selecting the appropriate stud type hinges on the environmental factors and specific mechanical demands associated with the project at hand.
Capacitor Discharge (CD)
Capacitor Discharge (CD) weld studs are specifically engineered for quick and efficient attachment, particularly suited for use with thin metal sheets where conventional welding methods might cause warping or damage.
These studs employ a high-energy capacitor discharge system that instantaneously releases energy concentrated at the weld point, creating a strong bond without significant heat to help preserve the integrity of the thin material.
- CD Threaded: Standard threaded CD studs are favored for their rapid, mark-free fastening across diverse applications. The threading allows for components to be easily attached and detached, making these studs ideal for scenarios requiring adjustability or temporary fastenings, such as in covers, housings, or removable panels.
- CD Non-threaded: Often utilized as locators or stop pins, CD non-threaded studs serve essential roles in assembly processes, including Poka Yoke (mistake-proofing) techniques. Their main function is to ensure components are correctly positioned before permanent attachments are made, thereby preventing assembly errors and ensuring consistency in manufacturing processes.
- CD Tapped: These studs are invaluable for adding threaded bosses to thin gauge materials, allowing for bolt or screw attachments without marking or damaging the reverse side of the material. This capability is particularly useful in automotive, aerospace, and electronics industries where the integrity and aesthetics of exposed surfaces are paramount.
- CD Collar: Designed to provide stand-offs for thinner gauge materials, CD collar studs create necessary space or separation between components, such as in electrical assemblies where insulation from other conductive materials is required. Their application is key to preventing contact that could lead to short circuits or mechanical interference.
When it comes to projects involving welding delicate material, CD weld studs stand out as an exceptional choice due to their ability to provide reliable fastening without jeopardizing the integrity or visual appeal of the delicate material.
Each of these distinct types is carefully engineered to fulfill a specific function, all while ensuring flexibility and reliability in thin metal applications.
Consulting With Welding Experts
If you’re still unsure of what type of stud weld to use in your respective project, you should reach out for the guidance of an experienced welding engineer or supplier to help you.
They can help guide your decision based on factors such as the compatibility of the materials you’re welding, the welding method you’re employing, and any specific application requirements. They may also offer specialized stud weld training to help you nail the perfect weld stud.
Trust Image Industries for All Of Your Stud Welding Needs
To choose the most suitable weld studs for your particular project you should carefully consider the applicable key factors.
Partnering with a seasoned supplier like Image Industries Inc. can further streamline your selection process. Image Industries offers a comprehensive range of weld studs, stud welding fastening systems, and stud welding accessories to tackle any project you may have. On top of this, they use their wealth of experience to provide expert guidance and to help tailor solutions to your specific needs.
Get in touch with Image Industries Inc. today online or by calling them toll-free at 1-(866)944-0335 or request a quote online to explore their extensive product offerings and consult with their experts to ensure that your next project is a real success.
Building lasting bonds since 1976.
Providing superior stud welding and stud welder parts and equipment isn't enough. We also strive to deliver better service and unmatched expertise. And that's exactly what we've been doing for more than 40 years.
Read About Our History