Blog
The Different Types Of Weld Studs And Their Uses
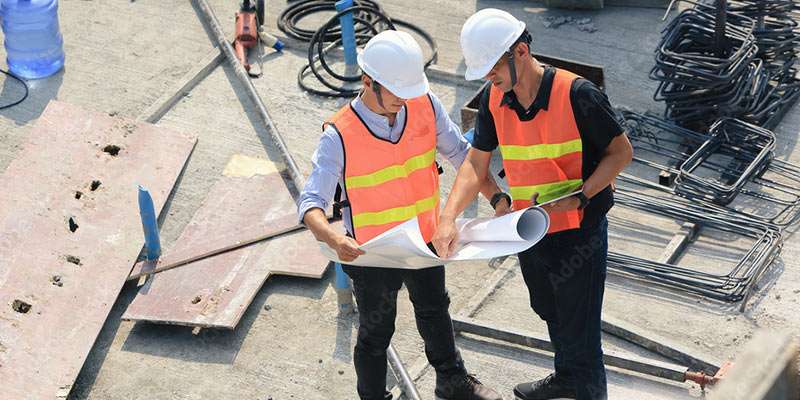
Stud welding is the technology of joining metal studs of all different sizes and applications to substrates made of a similar metal using a high current arc of electricity. This arc produces enough heat to melt the fastener base and the mating substrate. Once a molten pool forms, the fastener is then plunged into the pool, causing the current to stop and the molten metal to re-solidify so that both parts are joined by an even stronger weld.
Stud welding is used in all metalworking industries. Since it is a single-side fastening process, it is perfect for cosmetic applications requiring fasteners, including ATM machines, elevator buttons, and cooktops. Stud welding is well-favored partly due to the speed at which it can be carried out. Stud welding times range from .006 to 1.25 seconds depending on the size of the fastener.
The speed, however, does not impact the reliability or strength of the resulting joints. In fact, the weld is actually stronger than either the stud or its mating substrate. Unlike bolts with a peripheral weld or “clinch” fasteners that are pressed in place, stud welds create fully cross-sectional welds that achieve relatively higher strengths.
What Are Weld Studs?
Weld studs are cold-formed or CNC machined metal parts designed to be stud welded to substrates made of similar metal. Weld studs take less time to install than fasteners that require drilling, screwing, punching, or tapping. A weld stud loads into a compatible stud welding gun, and the gun connects to a stud welder that delivers current to the stud. This current melts the base of the stud along with an area of the workpiece to fuse them together and create a weld.
Weld studs can be threaded to be used as a fastener or unthreaded to be used as a pin or locator. They can be made from low-carbon steel, stainless steel, aluminum, and even nickel-iron alloys. Their diameters can range from approximately .100” (4mm) up to 1” (25mm), with lengths ranging from .25” (6mm) and up. They can be straight, bent and even have flanges and collars to be used as stand-offs and can be internally tapped.
What Are The Types Of Weld Studs?
Here are the different types of weld studs and their uses:
1. Drawn Arc Weld Studs
As a company specializing in welding studs and stud welding equipment, Image Industries offers a much greater range of studs than our industry competitors. With our ability to work with your design and engineering team to create custom-drawn arc weld studs to meet your project’s needs and specifications, we can provide the ideal parts for your projects in both high volume and smaller sourcing needs.
We specialize in many different categories of weld studs, such as drawn arc weld studs and CD weld studs, as well as specialized studs for cable management and hydraulic fittings. In this article, we highlight a few of our most popular drawn arc welding stud options.
Image offers a broad range of studs to match any application that you need completed.
- Full Thread: Fully threaded arc studs are the most common arc stud and are used in thousands of different applications
- Partial Thread: Partially threaded weld studs provide more shear than the same size fully threaded stud
- No Thread: No-thread studs are typically used in equipment manufacturing and fabrication to form handles, stops, and locators. These come in a range of sizes, and, like most welding studs, they are available in mild and stainless steel.
- Collar Stud: Collar Studs are usually used as standoffs for wire routing, plate spacing etc.
- Full Base: Full base studs are used when maximum shear is needed for a given thread size
- Reduced Base: Reduced base studs are used when the application design does allow clearance for the collar of weld flash
Threaded Weld Studs
The vast majority of our on-hand inventory is threaded weld studs. These studs are used to fasten or join a base workpiece to another part or component. The threading on the stud allows a nut to be used to fasten two pieces without drilling a hole or needing to secure the opposite end of the stud to tighten the nut.
2. Capacitor Discharge Weld Studs
Capacitive Discharge (CD) stud welding is a proven technology that has been in use for over 50 years. The broad range of use and applications is appealing to those looking for a fast, easy, and versatile process. The equipment is generally small and operates off of low voltage (110V or 240V in North America, 220V in Europe, for example). Fasteners designed for CD welding typically have a flange formed on the weld end in conjunction with a tip that initiates the discharge arc and subsequently vaporizes once electrical current is applied. The re-solidified flange enables a strong weld.
To perform a weld using a CD stud welding system and a CD weld stud, you begin by loading a weld stud into its appropriately sized chuck or collet attached to the welding gun and then placing the welded end against the metal substrate it will be welded to. The power supply will then communicate with the gun, raise the stud slightly from the substrate, and send an electrical current stored in the capacitor to the metal piece and fastener. The heat resulting from this arc melts the metal substrate as well as the tip and collar of the fastener. For the fraction of a second the fastener end and mating substrate are molten, a spring within the gun plunges the fastener into the substrate strongly fusing them together as they cool.
At Image Industries, orange of Capacitor Discharge weld studs includes mild steel and stainless steel studs, aluminum alloy studs, and lead-free brass studs. Our CD weld studs are available in threaded, unthreaded, tapped, collar, and internally threaded forms, making them ready to be used in any type of CD welding project.
3. Construction Weld Studs
In the construction industry, headed stud anchors are stud welded onto steel, and the concrete poured on top creates a solid, durable hold that is effective as well as easy.
However, it is also possible to use our headed stud anchors for precast concrete. This is most commonly seen in construction where steel beams and framing is used in conjunction with concrete tilt-up walls.
Image Industries offers three construction weld stud products:
Options in Anchors
Shear connector studs and headed anchor studs are used in construction to attach two different materials, typically concrete and steel. They are essential in bridge construction and building construction where the headed part of the stud forms the anchor into the concrete, joining the two materials together, forming a composite construction and providing major cost savings.
The most common options in a headed stud anchor used in precast concrete will be either mild steel or stainless steel. The specific length and body diameter will be determined by the specific applications for the job. This, in turn, will be calculated to include the maximum yield strength as well as the maximum yield shear that will be present.
Typically, headed stud anchor sizes and diameters will also vary based on the specific placement or type of precast concrete structure. Most are three to eight inches in length and are patterned in specific groups to address load capacity requirements.
Issues that have to be carefully considered when using a headed stud anchor in a pre-cast construction project include concerns about the concrete breakout and pry-out. This is most commonly associated with free edges and shear force that is directed away, but with proper placement of the anchors as well as consideration for the specifics of the design, these issues can be addressed.
4. Advanced Process Weld Studs
Advanced Process studs are often used for short-cycle, gas arc, or robotic applications. These products include both threaded and no-thread varieties. Advanced Process threaded studs are often used for short cycle, gas arc or robotic applications, whereas Advanced Process non-thread studs are only used for short cycle or gas arc applications.
5. Weldable Cable Management Mounts
Cable management has been a problem for as long as there have been cables. But now, there is a breakthrough of cable management solutions that are fast, affordable and simple.
QuikLinx Cable Tie Mounts
Instead of using a weld stud, screw, or adhesive, it is possible to install high-tech QuikLinx metal cable tie mounts almost instantly with arc stud welding technology. With different options and designs, including those for use with short cycle and gas arc stud weld processes, these cable tie holder designs can be applied in a fraction of a second, providing a solid weld between the mount and the metal surface. With the ability to apply these using a stud weld system at about 3 seconds per cable tie mount, this is a cost-effective, fast, and easy way to run a cable across structural components that were extremely challenging to work with in the past.
These small-sized mounts come with wings that allow for the cable tie to be inserted through the mount to hold the cable or cable assembly solidly in place. Additionally, we provide the option of a single shot system, which is ideal for lower volume applications for metal cable tie mounts, or a magazine-fed system that is effective for rapid and exclusive installation of the tie mounts.
CD Wire Tie Studs
When it comes to cable management products, Capacitor Discharge (CD) wire tie studs are the superior option for securing cable tie bases as compared to common adhesives or screws. Their use ranges across a variety of workplace environments, from cables for heavy machinery to standard desk space equipment. They offer quick wire security so you can focus on work without worrying about causing damage or accidents.
CD Ground Studs
CD ground studs can be used wherever a ground touchpoint is required. Image Industries offers CD ground studs that are designed to make it easy to establish a ground connection where you need it.
HD Wire Tie Studs
HD wire tie studs are a heavy duty gas arc solution that has the benefit of being able to weld through paint (black paint is recommended).
6. Hydraulic Cylinder Ports
Image Industries offers the following hydraulic port welding products:
- Hydraulic weld ports
- Hydraulic weld port plugs
- Tube line clamps
Companies have been manufacturing welded hydraulic cylinders for decades. Many different stud welding techniques have been used, including:
- MIG Welding
- Stick Welding
- Friction Welding
We developed a stud welding method that enhances the welding of the bosses or ports on hydraulic cylinders. Image’s hydraulic port welding process has many advantages for hydraulic cylinder manufacturers:
Fast Process
Because the stud weld process is fast (less than 1 second arcing time), the throughput is significantly enhanced compared to traditional hydraulic cylinder port welding.
Low Distortion
Because the stud weld process is fast, the amount of heat input into the tubing is low. This low overall heat input greatly reduces “egging” or ovality in the tube wall. This means that tube finishing can be done before port welding or that secondary post-port welding operations can be eliminated.
Fewer Leaks
Offering a full cross-sectional weld as opposed to a circumferential weld, the leak performance of the stud weld port is superior to conventional boss welding. The entire face of the bottom of the port is welded to the tube instead of the outside edge.
Reduce Tube Wall Thickness
Because of reasons 1, 2 & 3 above, many cylinder manufacturers have been able to reduce the tube wall thickness. One manufacturer went from a 7mm wall to a 5mm wall. This has saved that manufacturer tons of steel each year.
Saves a fitting
Often, manufacturers will weld an NPT fitting to the tube, and then the assembly will install a right angle JIC, O-ring boss, or O-ring face seal adapter into the NPT boss welded to the tube. Assembly is then tasked with trying to line up the adapter to a specific orientation to support a specific tube routing. This can mean loose or overly tight fittings. The stud weld port can be manufactured with the desired final fitting and welded at the exact orientation. This eliminates the adapter fitting and speeds up assembly.
7. Insulation Pins
Insulation pins are used to install insulation on the outside or inside of furnace shells as well as secure insulation in steel buildings. Insulation pins can also be attached to cloth seals to protect equipment from heat. There are several different kinds of insulation pins for welding, Image Industries offers the following:
- CD insulation pins
- Cupped head pins
- Double pointed insulation pins
Discuss Your Stud Welding Needs With Image Industries
If you are in need of a specific type of weld stud or are unsure which type you need, reach out to Image Industries. Our team of stud welding experts has years of experience providing manufacturers and welders with several products to meet their welding needs. For more information, call Image Industries at (866) 944-0335 or request a quote online today.
Building lasting bonds since 1976.
Providing superior stud welding and stud welder parts and equipment isn't enough. We also strive to deliver better service and unmatched expertise. And that's exactly what we've been doing for more than 40 years.
Read About Our History