Blog
Stud Welding vs Spot Welding: Understanding the Differences
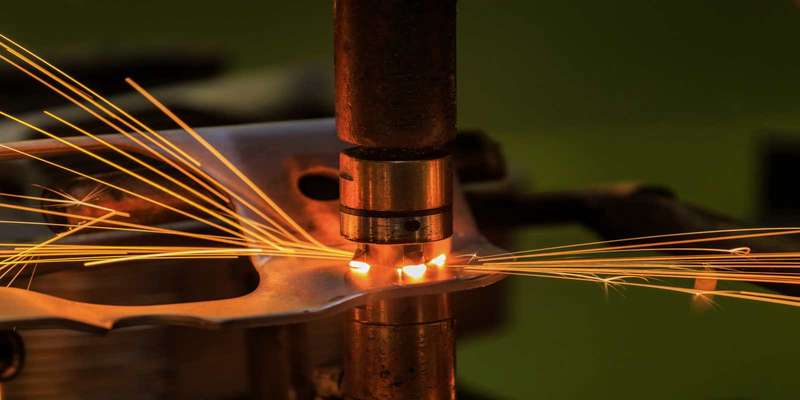
An Introduction to Stud Welding and Spot Welding
Welding technologies have come a long way, and they play a critical role in various industries—from construction and manufacturing to automotive and aerospace. Two prevalent welding techniques are stud welding and spot welding. While both serve the primary purpose of joining metal parts, the techniques, applications, and results differ substantially.
The Basics of Stud Welding: Process and Applications
Stud welding involves securing a fastener, usually known as a stud, to a workpiece. An arc is formed at the stud's end, melting part of it and the area where it will attach to the workpiece. This molten metal solidifies, creating a strong, full-penetration weld quickly. At Image Industries, we've even developed Smart Weld™ digital arc stud welding equipment that brings efficiency and precision to the process.
Stud welding is prevalent in various industries, including construction, shipbuilding, and electrical enclosures. It is often used for securing electrical grounding, mechanical fasteners, or as a part of a larger assembly process.
The Fundamentals of Spot Welding: Process and Use Cases
In contrast, spot welding employs electrical resistance to generate heat between two metal sheets that need to be joined. The sheets are clamped together and an electric current is applied to create a welded 'spot.' This method is often used in automotive manufacturing due to its ability to quickly join two overlapping pieces of metal without requiring the use of additional material, such as a stud.
Spot welding is highly effective in assembly-line processes and is often used to join sheet metals in the fabrication of automotive body parts, electrical enclosures, and even some household appliances. Its high-speed operation makes it ideal for mass production.
Understanding the Key Differences at a Glance: Stud Welding vs Spot Welding
In stud welding, the weld is made at a single point where a fastener is added to a workpiece, while spot welding joins overlapping metal sheets at multiple points. The former is ideal for creating strong, long-lasting welds and is more versatile in the types of materials that can be used. Spot welding is quick but may not be as strong as stud welding.
Detailed Comparison: Stud Welding vs Spot Welding
Diving deeper into these techniques reveals that they are designed for entirely different sets of needs and offer varied levels of quality, efficiency, and adaptability. Below we elaborate on the differences between stud welding vs spot welding.
Analyzing the Quality and Strength of Welds: Stud vs Spot
Stud welding is often regarded as superior in terms of the strength and durability of its welds. This method allows for full penetration, creating a bond that often has the same strength as the base material. It leaves a clean weld, requiring no additional cleaning or grinding, thus saving time and resources.
Spot welding, although fast, doesn't usually achieve full penetration. This limitation means that while it's sufficient for some applications, it's not suitable for structural work that demands a high-integrity bond.
Time and Efficiency Considerations in Stud Welding and Spot Welding
When efficiency is the priority, each method has its place. Stud welding is often faster for single-point applications and provides a clean weld that doesn't require additional finishing, thereby reducing labor and time costs. On the other hand, spot welding shines in high-volume, assembly-line environments where hundreds of welds need to be made in quick succession.
Comparing Material Suitability and Limitations: Stud Welding vs Spot Welding
Stud welding is highly versatile, able to weld various types of materials—ferrous and non-ferrous alike. Spot welding is generally more limited, best suited for low-carbon steels and other electrically conductive materials.
Choosing Between Stud Welding and Spot Welding
The decision between stud and spot welding hinges not only on the specific needs of your project but also the long-term implications for durability, efficiency, and cost.
Factoring in Project Requirements and Specific Use Cases
The choice between stud and spot welding often boils down to project-specific needs. For applications requiring robust, durable bonds—such as construction or heavy machinery—stud welding is usually the better option. Spot welding is more appropriate for mass production scenarios where the highest strength is not required.
Cost-effectiveness and Resource Utilization: Stud Welding vs Spot Welding
Although the initial investment for stud welding can be higher, its durability, speed, and minimal need for post-weld cleaning often make it more cost-effective in the long run. Spot welding may have a lower upfront cost but may require additional steps like grinding or cleaning, adding to the overall expense.
Making the Most of Your Welding Operations with Image Industries
At Image Industries, our commitment to quality, lasting bonds extends beyond our products to the lasting relationships we build with our clients, ensuring that we provide superior cable management ties and solutions and unmatched service and expertise.
As the global leader in the design and manufacturing of weld studs and stud welding equipment, we will continue to help our clients thrive in a connected world. To talk with our experts about your next project or challenge, get in touch with us here or call us at (800) 722-7883.
Building lasting bonds since 1976.
Providing superior stud welding and stud welder parts and equipment isn't enough. We also strive to deliver better service and unmatched expertise. And that's exactly what we've been doing for more than 40 years.
Read About Our History