Blog
How Weld Studs Improve Structural Integrity in Infrastructure Projects
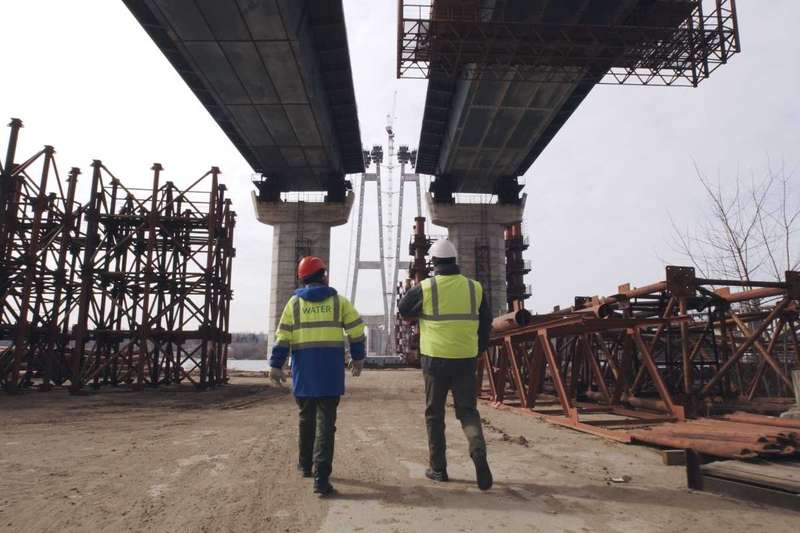
The Essential Role of Weld Studs in Infrastructure
A crucial aspect of infrastructure projects that should demand priority attention is ensuring the structural integrity of your weld studs, as they play an integral role in enhancing infrastructure projects' overall strength and stability. Weld studs come in various designs, measurements, and materials, each built for a specific purpose. As leaders in weld studs and their application, we'll dive into the significance of weld studs in structural connections and how they contribute to improved safety and durability in various applications.
Introduction to Structural Integrity in Infrastructure Projects
The overarching goal of any infrastructure project is to create safe and reliable structures capable of withstanding various loads and environmental conditions. Structural integrity ensures that the elements within the infrastructure maintain their shape and function as intended throughout their design life.
Ensuring the structural reliability of your weld studs and their application to construction projects is crucial to avoid catastrophic failures that could lead to costly repairs, downtime, or, in extreme cases, endanger human lives.
The Importance of Weld Studs in Structural Connections
Weld studs help develop solid and reliable connections within an infrastructure. These specialized fasteners, typically made of metal, are welded to a base material, creating a robust joint. Their applications range from securing beams, columns, and trusses to attaching various fixtures and components to the structural framework.
Advantages of Weld Studs in Structural Connections
1. High Load-Bearing Capacity
Weld studs provide exceptional load-bearing capacity due to their secure attachment to the base material. This property makes them ideal for carrying heavy loads and distributing forces evenly throughout the structure, preventing localized stress concentrations.
2. Quick and Efficient Installation
Stud welding offers rapid and efficient installation, reducing construction time and labor costs. The process involves minimal preparation and can be performed with automated equipment, making it suitable for large-scale projects.
3. Enhanced Structural Strength
By effectively joining structural elements, weld studs improve the overall strength and stability of the infrastructure. This results in a more resilient and durable structure capable of withstanding dynamic forces like wind, seismic activity, and heavy traffic loads.
4. Corrosion Resistance
Weld studs made from corrosion-resistant materials can significantly enhance the infrastructure's longevity, especially in environments exposed to moisture, chemicals, or marine conditions.
5. Versatility in Design
Weld studs come in various sizes and materials, providing flexibility in design and allowing engineers to tailor connections to specific project requirements.
Enhanced Safety and Durability with Weld Studs
In an infrastructure project, weld studs are secured to help ensure robust connections between structural elements and reduce the risk of sudden failures or collapses. This makes weld stud design and material choice critical as a safety and durability feature on a project. Additionally, the high load-bearing capacity and corrosion resistance prolong the service life of the infrastructure, minimizing maintenance needs and associated costs.
Examining Weld Studs in Action
Weld studs are used in a variety of different construction projects and purposes. Whether you're supporting a bridge or strengthening a high-rise building, project managers depend on weld studs to secure their structure. They are pivotal in enhancing the structural integrity of various infrastructure projects, ensuring their safety, stability, and longevity.
Bridge Construction: Weld Studs in Load-Bearing Structures
Bridges are critical transportation links that withstand heavy loads, traffic vibrations, and environmental stresses. Weld studs are extensively used in bridge construction to create load-bearing structures capable of withstanding these demanding conditions.
Benefits of Weld Studs in Bridge Construction
- Strength and Load-Bearing Capacity: Weld studs provide a reliable connection that distributes loads efficiently, ensuring the bridge's structural stability even under heavy traffic.
- Corrosion Resistance: Corrosion-resistant materials for weld studs contribute to the bridge's longevity, especially in areas exposed to harsh environmental conditions.
- Ease of Installation: The quick and efficient installation process of weld studs minimizes construction time, reducing the overall project cost.
High-Rise Buildings: Enhancing Stability with Weld Studs
High-rise buildings present unique challenges due to their height and exposure to wind and seismic forces. Weld studs enhance these tall structures' stability and structural integrity.
Benefits of Weld Studs in High-Rise Buildings
- Seismic Resistance: Weld studs enhance the building's ability to dissipate seismic energy, reducing the risk of structural damage during earthquakes.
- Fire Resistance: When using fire-resistant materials, weld studs can improve the building's fire resistance, contributing to occupant safety.
- Precision and Stability: Accurately placing weld studs ensures precise connections, resulting in a stable and reliable high-rise structure.
Tunnels and Highways: Ensuring Longevity with Weld Studs
Tunnels and highways are subject to significant stress from vehicular loads and environmental factors. Weld studs are employed in these projects to ensure the durability and safety of these transportation infrastructures.
Benefits of Weld Studs in Tunnels and Highways
- Durability: Weld studs enhance the overall durability of tunnels and highways, ensuring they can withstand heavy traffic loads over extended periods.
- Easy Maintenance: Weld studs contribute to effortless and efficient maintenance, as damaged components can be replaced or repaired quickly.
- Cost-Effectiveness: Using weld studs reduces long-term maintenance costs, making infrastructure projects more economically viable.
The Science Behind the Strength: Why Weld Studs Work
Weld studs are specialized fasteners, typically made of metal, welded to a base material to create a robust and reliable joint. Understanding how weld studs work and the different welding methods involved is essential for ensuring their successful application in construction.
The Welding Process: A Deep Dive into Drawn Arc Stud Welding
Drawn arc stud welding is a versatile and efficient process that involves joining weld studs to base materials through an electric arc. The process can be broken down into the following key steps:
- Preparation: The welded surface of a structure, whether steel, stainless steel, aluminum, or other metals, must be cleaned and prepared to ensure optimal weld quality. Any contaminants or oxides on the surface are removed through brushing, grinding, or other suitable methods.
- Positioning: The weld stud is positioned precisely on the prepared surface at the desired location for attachment.
- Arc Initiation: A stud welding gun is used to initiate an electric arc between the tip of the weld stud and the base material's surface. The arc generates intense heat, melting the stud and the base material around the welding point.
- Stud Placement: As the molten pool is formed, the stud is rapidly plunged into the pool and held in place under a specified amount of force. This process ensures proper fusion between the stud and the base material.
- Solidification: The molten material solidifies quickly, forming a strong metallurgical bond between the weld stud and the base material.
Material and Design: The Anatomy of a Weld Stud
Choosing materials for weld studs is crucial in determining the strength, durability, and performance of the welded connections. Some common materials used for weld studs include:
- Carbon Steel: Carbon steel weld studs offer excellent strength and are widely used in various applications.
- Stainless Steel: Stainless steel weld studs provide superior corrosion resistance, making them suitable for projects in corrosive environments.
- Aluminum: Aluminum weld studs are lightweight and commonly used in projects where weight is critical.
- Copper: Copper weld studs are employed in specialized applications, such as electrical and grounding connections.
Compliance and Standards: Ensuring Quality in Weld Studs
Compliance with material standards and regulations is essential to ensure the quality and safety of weld studs used in infrastructure projects. Some key considerations include the following:
- AWS D1.1 and D1.6: These American Welding Society (AWS) standards provide guidelines for structural welding of steel and stainless steel, commonly used materials for weld studs.
- ISO 13918: This international standard specifies the requirements for stud welding with drawn arc stud welding equipment, ensuring consistent quality and performance.
- EN 14555: European standard for the execution of steel structures, including requirements for stud welding.
- Industry-Specific Standards: Different industries and applications may have specific standards and regulations governing the use of weld studs, such as automotive or aerospace industries.
Adhering to these material compliance and regulation standards guarantees the integrity and reliability of the weld stud connections in infrastructure projects.
Delivering Dependability with Image Industries
The quality of your weld studs is crucial as they provide robust connections, enhanced load-bearing capacity, and corrosion resistance, contributing to the safety, stability, and longevity of constructed elements. To ensure your infrastructure project benefits from the highest-quality weld studs, contact the professionals at Image Industries or give us a call at (847) 793-1943. We offer several decades of developing industry-grade stud welds that will meet the highest performance and safety standards in your construction endeavors.
Building lasting bonds since 1976.
Providing superior stud welding and stud welder parts and equipment isn't enough. We also strive to deliver better service and unmatched expertise. And that's exactly what we've been doing for more than 40 years.
Read About Our History