Blog
How to: Drawn Arc Welding Aluminum Weld Studs
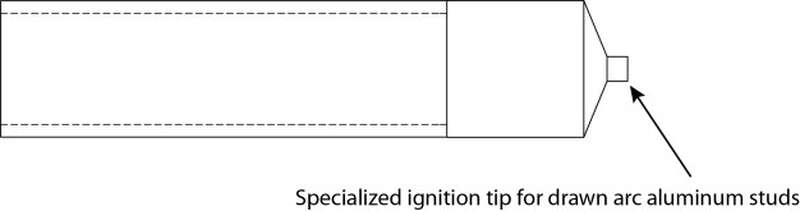
Drawn arc welding aluminum studs is difficult. It can be done; it is more difficult than steel and steel alloys. When compared to steel and its alloys, aluminum has a narrower tolerance for set up and weld parameters. Once you find acceptable parameters even small drifts of those parameters can cause the process to fail.
Like aluminum CD stud welding the material must be properly prepared and cleaned. Oxides and oils can interfere with successful aluminum stud welding. Cleaning the surface with a STAINLESS STEEL brush will remove the oxide layer. After brushing, wiping down with a non VOC cleaner is recommended.
Using drawn arc with aluminum weld studs REQUIRES a shielding gas. Most commonly used is 100% Argon (Ar). However, Ar/Helium (He) mixes (25% to 75% He) and 100% pure He can also be used. He has greater arc ionization energy as well as thermal conductivity. This results in greater heat at the weld zone benefiting aluminum stud welding. In most facilities performing welding Ar is readily available and He is not so most users settle for 100% Ar. If you find yourself having trouble with 100% Ar remember that a Ar/He mix is an available option.
It is also critical that the correct accessories are used for stud welding Aluminum. The most successful aluminum stud welding uses ceramic ferrules as well as the shielding gas. There are specialized foot pieces that distribute the shielding gas as well as hold the ceramic ferrule around the aluminum weld stud. Image Industries has the necessary accessories to meet your aluminum arc welding applications.
Another consideration is the stud tip design. Aluminum studs should have an extra “tip” on the end. This small sized extra tip burns away rapidly. Once the tip has burned away the arc length is effectively longer than it would have been otherwise. The longer arc length creates a higher voltage at the weld which increases the heat at the weld zone.
The final appearance of a drawn arc welded stud will not be as aesthetically pleasing as a steel stud weld. Also, the visual indicators common to steel stud welding do not apply. The flash ring around the base of an aluminum stud is not a good indicator of weld quality. The best way to verify quality welds is to bend test or torque test pre-production samples. Once optimum parameters have been determined it is recommended that periodic in-process checks be performed to ensure that the weld quality is maintained.
If the procedures are followed and the operator is diligent, then drawn arc aluminum stud welding can be a robust process. If you have questions about aluminum stud welding please feel free to contact your sales representative or the factory for trouble shooting.
Building lasting bonds since 1976.
Providing superior stud welding and stud welder parts and equipment isn't enough. We also strive to deliver better service and unmatched expertise. And that's exactly what we've been doing for more than 40 years.
Read About Our History