Blog
Fundamentals of Stud Welding Techniques
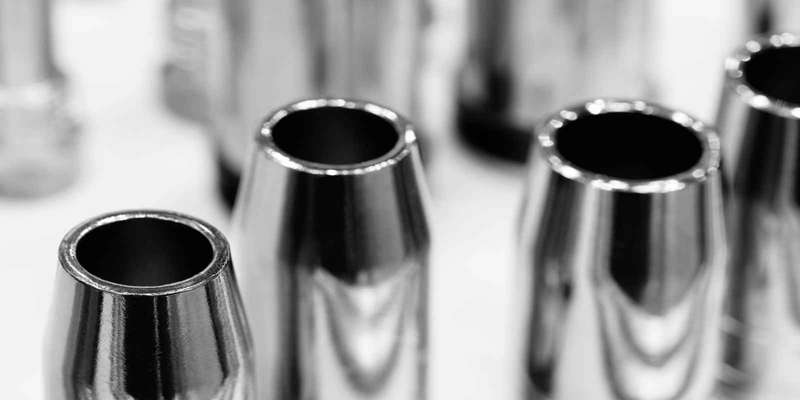
Stud welding is a highly efficient and versatile method of joining metal parts that’s used across an array of industries. In this article, we're going to give you a solid overview of stud welding, breaking down the fundamental components of a stud welding system and the various methods that are used in the stud welding process.
Having a solid foundational understanding of these techniques can help you improve your welding projects and deliver strong, reliable connections. We'll cover everything from the basics to more advanced applications, providing you with the essential knowledge to make the most of stud welding.
The Fundamentals of Stud Welding
Stud welding is a process that involves joining a metal stud to a workpiece, typically a base metal, by creating an arc between the stud and the workpiece.
Uses
It’s used across different heavy industries thanks to its efficiency and ability to quickly produce strong, consistent welds. The applications of stud welding are diverse, ranging from securing insulation materials to structural components and even electrical grounding.
Benefits
The benefits of stud welding include its speed, reduced need for secondary operations, and labor savings since a certified welder isn’t required. Stud welding also provides high-strength joints with minimal distortion of the base metal, making it ideal for applications where precision and strength are important.
Technique
To help guarantee the integrity of the weld, you want to make sure that you’re employing the proper stud welding technique. After all, using poor technique when welding can result in weak welds, which may lead to potential failures in structural applications and have devastating results.
Some important factors to keep in mind include proper alignment, appropriate welding parameters, and the use of the right equipment.
Considerations
Some common considerations in stud welding include dealing with surface contaminants, maintaining correct positioning, and guaranteeing a consistent supply of power.
Overcoming these possible issues involves thorough surface preparation, precise equipment setup, and regular maintenance of welding tools. Operators can achieve optimal results to get strong, reliable welds every time by carefully adhering to best practices when welding.
The Role of Weld Studs and Ferrules
There are different types of weld studs, each with its own advantages and uses, which include threaded, unthreaded, and shear studs.
Threaded studs are often used when a strong mechanical connection is needed, such as in structural applications or securing components that may need to be removed or replaced. Threaded studs offer versatility, allowing for easy disassembly and reassembly, and they’re ideal for applications where maintenance or future modifications are anticipated.
Unthreaded studs are typically used where a permanent, high-strength locator is required, such as in electrical connections or attaching insulation materials. Unthreaded studs provide a seamless, flush finish and are preferred where a smooth surface is necessary or where high shear strength is essential.
Ceramic ferrules play their own important role in the stud welding process. These small, ring-like components are placed around drawn arc weld studs prior to welding to contain the molten metal, preventing it from splattering and providing a clean, smooth weld. They also help to control the arc for consistent heat distribution and better weld quality.
The Components of the Stud Welding System
The components of a stud welding system work together in tandem to create strong, reliable welds. Properly understanding each component and its respective role is important to help you optimize your performance and achieve the best results in all sorts of different applications.
Power Source
In stud welding, the power source is needed to generate the necessary electrical current to the weld tool. The main types of power sources are Drawn Arc and Capacitor Discharge (CD).
- Drawn Arc power sources are widely used due to their ability to produce deep, strong welds suitable for heavy-duty applications.
- Capacitor Discharge (CD) power sources are perfect for applications requiring minimal heat input, making them suitable for thin materials and applications where the base metal must remain relatively cool.
Weld Tool/Gun
The weld tool or gun is the device that’s used to hold and weld the stud.
- Handheld weld guns are versatile and allow for manual mobility, making them suitable for varied tasks and on-site jobs.
- Automation weld guns, often mounted to a robot or cobot, provide more precision and consistency that prove to be important in high-volume production environments.
Going with the right tool is important to do since it can directly affect the quality and overall efficiency of the welding process.
Cables
Cables are core components that connect the power source to the weld tool and the workpiece itself.
- The ground cable is essential for completing the electrical circuit during welding. It makes sure that the current flows smoothly and consistently, which is essential for achieving a stable arc and a strong weld.
- Extension cables play a significant role in extending the reach of the welding system, providing the flexibility needed to work in larger or more complex setups. They enable operators to maintain consistent power delivery over greater distances, thereby enhancing the overall efficiency, reliability, and adaptability of the welding process.
Stud Welding Methods
Stud welding encompasses several techniques, each suited to different applications and materials. Two of the most commonly used methods are Drawn Arc Welding and Capacitor Discharge (CD) Welding, with each offering their own respective benefits and specific use cases.
Drawn Arc Welding
Drawn Arc Welding is a popular method that’s well-known across industries for its strength, reliability, and versatility.
The process begins by placing the stud against the workpiece and initiating an arc that melts both the stud and the base metal. The stud is then inserted into the molten pool, forming a durable weld as it cools and hardens. It’s ideal for heavy-duty applications requiring deep-yet-strong welds, such as in the construction and shipbuilding industries. This entire welding process typically takes less than ¾ second to complete, making it ideal for high-speed production environments.
There are also a few different variations of drawn arc welding, including Gas Drawn Arc and Short Arc Welding.
- Gas Drawn Arc Welding uses a shielding gas to keep the molten metal contaminant-free, resulting in cleaner welds along with improved durability. This variation proves to be particularly beneficial in environments where exposure to raw air could potentially compromise weld integrity.
- Short Arc Welding uses a shorter arc time, making it suitable for thinner materials where excessive heat input must be avoided. It provides more precise control over the entire welding process, which reduces the risk of burn-through and distortion.
Capacitor Discharge (CD) Welding
Capacitor Discharge (CD) Welding is a method that utilizes the rapid discharge of electrical energy stored in capacitors to create a weld.
This technique sets itself apart from drawn arc welding in its capability to weld studs onto materials that are thin or delicate while actively minimizing heat-induced distortions. A typical CD weld takes about less than ¼ second, similarly making it ideal for high-speed production environments.
There are two main subtypes of CD welding: Contact CD Welding and Gap CD Welding.
- In Contact CD Welding, the stud is in direct contact with the workpiece when the discharge occurs, resulting in an almost instantaneous weld. This method is perfect for applications requiring minimal setup time and maximum speed.
- Gap CD Welding, however, involves a small gap between the stud and the workpiece, which allows for a more controlled energy release and precise weld. This particular subtype is beneficial in situations where delicate materials or exact positioning are essential and for the welding of aluminum studs to aluminum substrates.
Stud Welding Specialists
Getting a handle on stud welding techniques is essential for producing high-quality and reliable welds that you can stand by.
With an in-depth understanding of welding methods, components, and best practices, you can actively enhance the quality of your welding outcomes. On top of this, keeping up with the latest advancements in stud welding technology is also important.
For the finest weld studs, stud welding systems, and accessories, check out Image Industries Inc. Our products and expertise can help you get the very best results out of all your welding projects.
Building lasting bonds since 1976.
Providing superior stud welding and stud welder parts and equipment isn't enough. We also strive to deliver better service and unmatched expertise. And that's exactly what we've been doing for more than 40 years.
Read About Our History