Blog
Exploring the Versatility of Weld Studs: Applications Across Various Industries
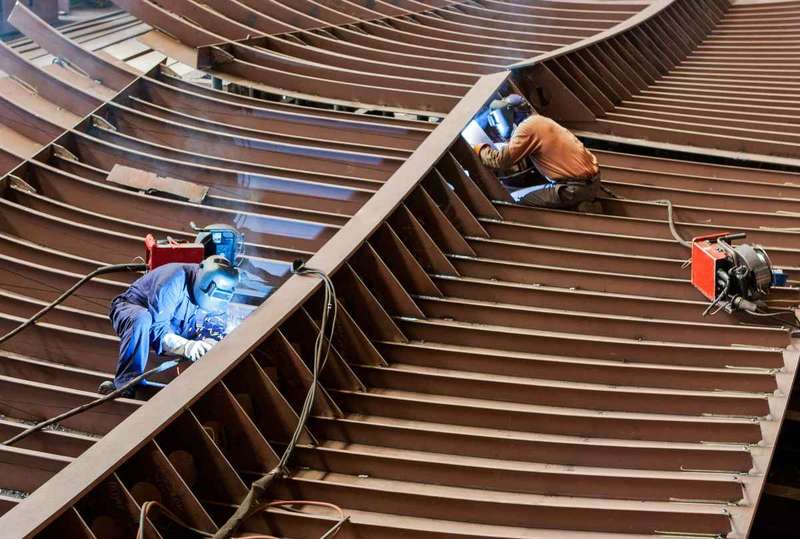
While they're indeed essential in the construction world, weld studs have a much broader range of applications. From the civil construction sites to the shipbuilding docks and even in the commercial trucking realm, these tiny components make a big impact.
The Power of Weld Studs in Structural Connections
Connections are the lifeline of any structure. How these connections are secured, their design, and the materials used are pivotal to a structure's longevity and safety. Weld studs emerge as an exceptional choice in this domain. Their combination of superior load-bearing abilities and versatility makes them unparalleled in securing these vital junctures.
Safety First: The Durability of Weld Studs
Safety is more than a buzzword when it comes to structural design – it's a mandate. Weld studs are crafted to endure, resisting the usual wear and tear that can compromise other materials. This not only prolongs the life of the structures they’re a part of but also adds an additional layer of safety for those who use or inhabit them.
Diverse Industries, Common Need: Structural Integrity
Whether securing vital components in compact construction machinery, ensuring stability in shipbuilding, or facilitating robust connections in commercial trucking vehicles, weld studs are indispensable. Their unparalleled load-bearing capacities are a testament to their strength, while their versatile design ensures a seamless fit across various applications. From enduring the weight of heavy machinery to resisting the corrosive marine environment, and bearing the relentless demands of long-haul trucking, weld studs consistently prove their mettle. Their adaptability and resilience make them an indispensable choice in a diverse range of scenarios.
A Glimpse into Weld Stud Applications
Compact Construction & Agriculture
In the world of compact machinery and farming equipment, durability is paramount. Weld studs ensure that agricultural tools remain robust, allowing farmers to work efficiently, and compact construction machinery to function optimally.
Key Applications for Weld Studs Include:
- Securing plow blades to tractors.
- Attaching components of compact loaders.
- Reinforcing joints in harvesters.
- Bolstering the chassis of utility tractors.
- Enhancing the structural integrity of bailers.
Cylinder Manufacturing
Hydraulic cylinder manufacturing requires precision components and assembly to ensure optimal safety and performance. Hydraulic port weld studs ensure cylinders are leak-proof compared to other porting options.
Key Applications for Weld Studs Include:
- Crafting hydraulic pistons for bulldozers or excavators.
- Preventing leaks around ports under high pressures.
- Securing hydraulic arms in backhoes.
- Reinforcing cylinder seals in hydraulic jacks.
- Bolstering the structure of cylinder assemblies.
Industrial Fabrication
As the backbone of modern industry, fabrication units require weld stud components that can withstand heavy use. Weld studs offer that reliability, ensuring the machinery and final products meet the highest quality standards.
Key Applications for Weld Studs Include:
- Attaching safety guards on conveyor systems.
- Fixing body plates of industrial crushers.
- Anchoring heavy-duty machinery to factory floors.
- Securing load-bearing beams in warehouses.
- Fastening external casings of rotary machines.
Civil Construction
Beyond skyscrapers and bridges, weld studs are instrumental in various civil projects, from roads to public utilities, guaranteeing longevity and safety.
Key Applications for Weld Studs Include:
- Securing guardrails on highways.
- Anchoring lighting fixtures in tunnels.
- Reinforcing steel beams in high-rises.
- Stabilizing barriers on bridges.
- Fixing sound barriers along expressways.
Electric Power & Nuclear
In these sectors where safety and reliability are of utmost importance, weld studs provide the structural assurance needed to maintain secure operations.
Key Applications for Weld Studs Include:
- Anchoring protective casings around nuclear reactors.
- Stabilizing components within hydroelectric dams.
- Fastening transmission towers.
- Securing high-voltage cables.
- Reinforcing barriers in power plants.
Shipbuilding
Facing the rigors of the marine environment, ships benefit from the strength and resilience of weld studs, ensuring the vessels remain seaworthy.
Key Applications for Weld Studs Include:
- Fastening deck plates on ships.
- Securing ship hulls against rough seas.
- Anchoring cargo hold doors.
- Reinforcing ship bridges.
- Fixing exhaust stacks on cruise ships.
Food Service
From equipment to food processing units, weld studs ensure everything stays in place, allowing for efficient service delivery.
Key Applications for Weld Studs Include:
- Anchoring large ovens and grills in commercial kitchens.
- Sealing large industrial freezers.
- Fixing storage racks in pantries.
- Stabilizing conveyor belts in bakeries.
- Attaching blades in industrial food processors.
Commercial Trucking
For vehicles that transport goods across vast terrains, weld studs provide the much-needed structural integrity, ensuring goods reach their destinations safely.
Key Applications for Weld Studs Include:
- Stabilizing compartments in refrigerated trucks.
- Reinforcing the chassis of long-haul trailers.
- Anchoring internal shelving in cargo vans.
- Fastening rooftop equipment on utility trucks.
- Securing tailgates on delivery trucks.
The Science Behind the Strength
Every weld stud's efficacy is the result of three components: the meticulous welding process, the stud's material and manufacturing process, and stringent quality standards.
- Welding Excellence: The drawn arc stud welding process is central to the strength of the weld between the fastener stud and the metal surface it is being applied to. When the proper stud welding equipment is used, and the welding parameters of current and weld time are set correctly, that weld area is stronger than either the fastener or the substrate.
- Material and Manufacture: Weld studs are commonly made from low-carbon steel, stainless steel, and weldable grades of aluminum, but can also be made from alloys including HY80, Inconel and Monel. Weld studs are typically manufactured by cold heading and/or CNC machining.
- Commitment to Standards: Abiding by industry standards, such as those set by the American Welding Society (AWS), assures consistent quality and safety.
Your Trusted Partner: Image Industries
If you are in need of a specific type of weld stud or are unsure which type you need, reach out to Image Industries. Our team of stud welding experts has years of experience providing manufacturers and welders with several products to meet their welding needs. For more information, call Image Industries at (866) 944-0335 or request a quote online today.
Building lasting bonds since 1976.
Providing superior stud welding and stud welder parts and equipment isn't enough. We also strive to deliver better service and unmatched expertise. And that's exactly what we've been doing for more than 40 years.
Read About Our History