Blog
CD Weld Stud Types, Applications, and Best Practices
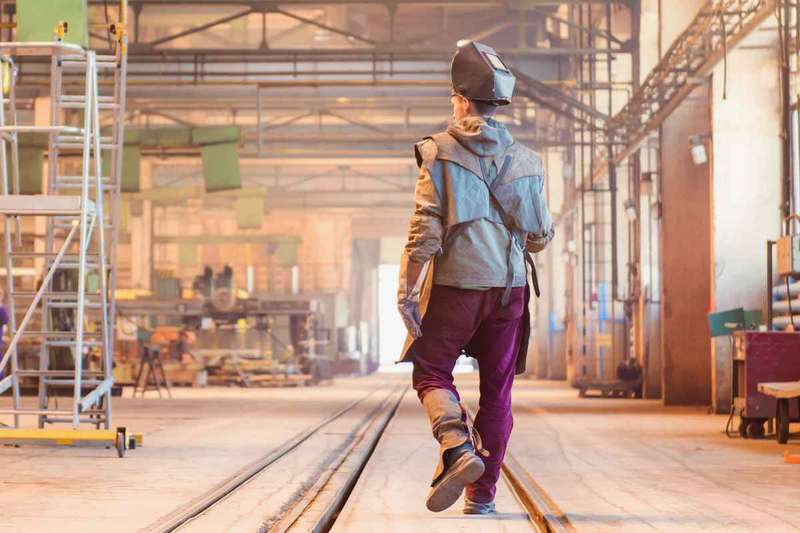
In the fabrication world, having secure and reliable fastener welds is paramount. One such component often utilized across many industries is the Capacitor Discharge (CD) weld stud. To understand their significance and ensure they are effectively used, it's crucial to dive into what they are, their designs, typical applications, and the necessary maintenance of the equipment that installs them.
What Is A CD Weld Stud?
CD weld studs are specialized fasteners, predominantly cold-headed or machined from stainless steel, mild steel, or aluminum. These studs possess a distinct design: a small projection in the center of the welded end of the stud when welded onto different metals using the CD welding method, aids in initiating a weld cycle that creates a connection in a fraction of a second that's stronger than each the fastener and the workpiece.
Different Designs of CD Weld Studs
CD weld studs come in various designs to suit specific applications. The most common types include:
- Threaded Studs: Featuring threads on one end opposite the welding point, they facilitate easy attachment of nuts or other threaded components.
- Unthreaded Studs: Lacking threads, these are utilized for projects demanding a flush finish. md5-868a73ed644988c1075a95b13881171f
- Wire Tie Mounts
Applications of CD Weld Studs
CD weld studs find their place in several applications thanks to their designed versatility and reliability. Some of the more common applications of a CD weld stud are:
Shipbuilding:
In shipbuilding, Their primary role involves securing essential components to both the ship's hull and its intricate interior structures. Brackets, stiffeners, and even cable hangers benefit from the reliable fastening provided by these weld studs. Due to the nature of ship construction, which involves layering multiple metal plates of varying thicknesses, a secure and lasting bond is paramount. CD stud welding offers this bond and does so with a speed and efficiency unmatched by traditional welding methods.
Automotive:
CD stud welding is crucial in the automotive industry for attaching components like brackets, clips, and reinforcements to vehicle bodies and frames. The key advantage is the speed and precision of CD stud welding, which can significantly streamline assembly line processes. CD stud welding reduces production time and costs by eliminating the need for additional fasteners or welding processes. Welds that are neat, clean, and low profile make them ideal for automotive applications where aesthetics and aerodynamics are important.
Commercial Food Processing Equipment:
Traditional assembly methods often require drilling, which can introduce risks of damage and compromise the aesthetics or functionality of the product. However, with CD weld studs, manufacturers can seamlessly integrate components, ensuring a tight bond and preserving the item's original design and integrity. This method extends the lifespan of appliances and cookware, promising longevity and consistent performance.
Best Materials For CD Weld Studs
The choice of materials is crucial for optimal performance. Mild steel weld studs are designed to be welded to steel workpieces, which are subsequently painted to provide corrosion resistance. Stainless steel weld studs on stainless steel workpieces offer corrosion resistance without paint or another barrier. Aluminum weld studs, manufactured from Alloy 5356, are necessary for welding to any aluminum substrate. Nonetheless, the selected material for your CD weld studs should align with the application's specific needs.
Importance Of CD Weld Stud Equipment Maintenance And Inspection
While CD weld studs don't need maintenance, the collets that hold them in the weld tool need to be replaced when worn, and the weld tool itself needs to be cleaned and maintained depending on usage. Equipment maintenance is paramount for optimal performance.
While the studs themselves are robust unless damaged, the stud welding equipment used to weld them is. Routine checks are critical to ensure that the weld is optimal. Moreover, the need for continuous operator training cannot be emphasized enough; ensuring best practices are at the forefront ensures longevity and optimal functioning.
Compliance with Industry Standards and Regulations
Familiarize yourself with the standards and codes relevant to your industry, ensuring that all welding activities meet or exceed these requirements. This involves utilizing approved materials, following recommended installation procedures, and regularly inspecting welds for compliance with specified quality standards. You should also keep detailed records of all welding activities and inspections to demonstrate compliance during audits or regulatory assessments. A commitment to adherence to industry standards not only ensures safety and quality but also establishes trust and credibility within your industry.
Repairing Minor Damages and Issues
Promptly addressing minor damages and issues is key to preventing more significant problems with your CD weld studs. Regular inspections should thoroughly assess small cracks, corrosion, or other imperfections when such issues are identified and repair or replace damaged studs as needed, adhering to manufacturer-recommended procedures. Corrective actions should be documented in your maintenance records.
Maintaining a Log of Maintenance and Inspection Activities
It's essential to maintain a detailed log of equipment maintenance and inspection activities, capturing dates, descriptions of actions taken, and the names of the personnel involved. This equipment's regular inspections and scheduled maintenance are critical to ensuring its optimum performance. By keeping a comprehensive record, you can ensure timely equipment maintenance, reducing the likelihood of unexpected breakdowns or disruptions.
Training Maintenance Personnel and Welders
The equipment used in the CD weld stud process requires personnel well-versed in its maintenance and operation. Training programs should equip maintenance staff and welders with knowledge of equipment best practices, safety procedures, and industry standards. The team can adeptly manage and maintain the equipment with ongoing training, ensuring smooth operations and consistent weld quality.
Get Professional CD Weld Stud Maintenance And Inspection Consulting From The Experts
If you have questions or need more information about CD weld studs or the equipment used to weld them, Image Industries is here to help. We're dedicated to providing solutions tailored to your specific needs. Contact us today or call us at 800-722-7883.
Building lasting bonds since 1976.
Providing superior stud welding and stud welder parts and equipment isn't enough. We also strive to deliver better service and unmatched expertise. And that's exactly what we've been doing for more than 40 years.
Read About Our History